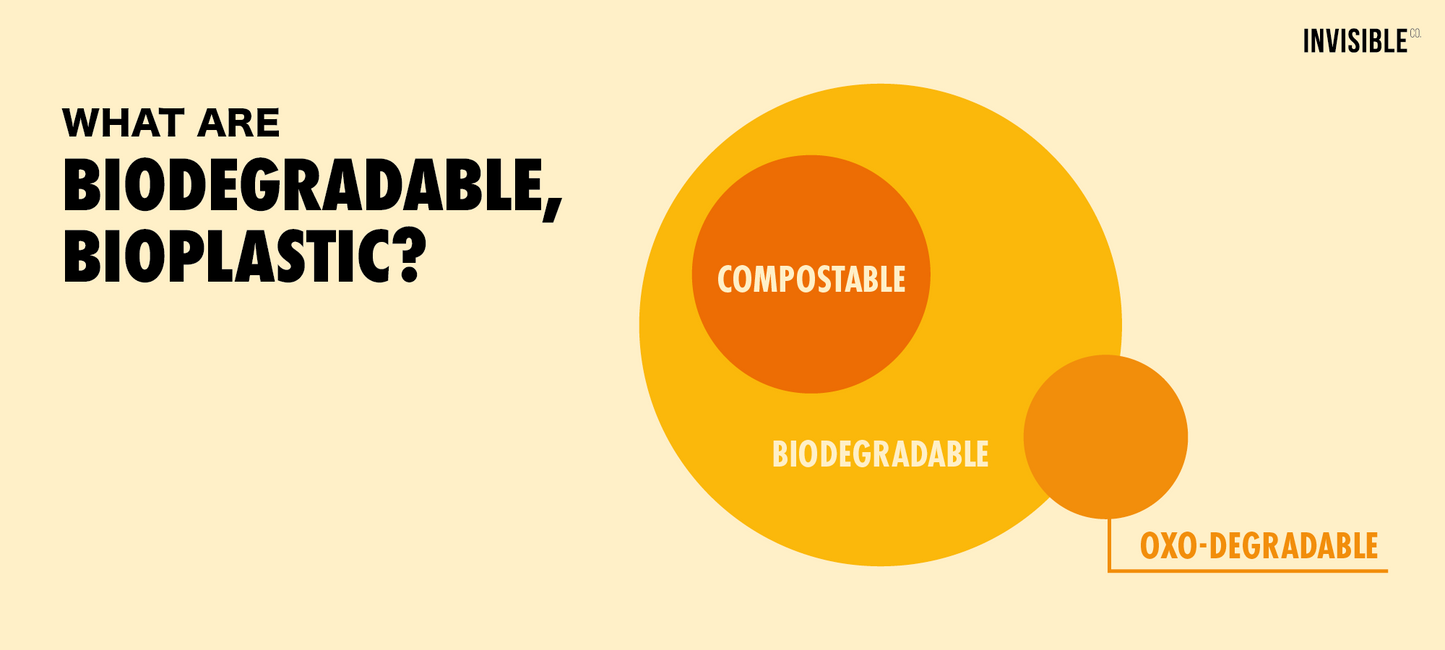
In today's packaging market, multiple options exist, ranging from packaging made of synthetic polymers to natural polymers and bioplastics. These materials may possess varying characteristics, such as compostability and degradability in different environments. With such a diverse range of choices, do you know how to distinguish and choose the right option for your brand? It is important to research the technicality and distinctions among these options.
While plastic is a widely discussed topic nowadays, however, everyone has different interpretations. Before we begin, let’s first understand what plastic means as a whole, exploring the proper and scientific definition of plastic.
What does plastic mean?
The term "plastic" refers to a wide range of synthetic, semi-synthetic, or natural materials that use polymers as a main ingredient. Polymers are used for their plasticity, making it possible for plastics to be moulded, extruded, or converted into flexible or solid objects of various shapes.
What are polymers?
But then what are polymers? And where to find them? Polymers are large molecules composed of repeating subunits called monomers.
Natural polymers are derived from renewable sources in nature, such as cellulose and proteins. Examples include starch, silk, and natural rubber.
Synthetic polymers, like polyethylene (PE), polypropylene (PP), and polyvinyl chloride (PVC), are human-made through chemical processes using petrochemicals or other raw materials.
In short, plastics can be synthetic, meaning they are human-made, or they can be derived from natural sources.
So it's important to note that there are different types of plastics for different applications, that not all plastics are created equal, and they can vary in their composition, properties, and environmental impact.

What means biodegradable?
“A material's ability to be completely converted into carbon dioxide, water, and biomass through the action of microorganisms, such as fungi or bacteria, found in the environment.”

These days we often read here and there information referring to biodegradable plastic, bags, or packaging, to understand what this means we need to look at what being biodegradable means. It refers to “a material's ability to be completely converted into carbon dioxide, water, and biomass through the action of microorganisms, such as fungi or bacteria, found in the environment.”
Currently, there are biodegradable plastics available in the market that possibly undergo these different types of degradation. For instance, certain plastics are designed to:
- Oxidatively degrade with the help of additives, while others
-
- Hydrolytic degrade when exposed to moisture
-
- Enzymatic degrade with the action of specific enzymes produced by microorganisms
-
- Photodegrade occurs when plastics break down under sunlight or UV radiation
-
- Thermal degradation takes place with the application of high temperatures.
Not all biodegradable plastics in production have been banned, but there may be regulations and restrictions on certain types of plastics to ensure environmental safety and compatibility with waste management systems.
What is Oxo-(bio)degradable plastics? Why is it banned?
One of the most popular biodegradable plastics is Oxo-biodegradable plastics (OBP). As most would be surprised to know, Oxo-biodegradable plastics (OBP) are conventional plastics like polyethylene (PE) that have been augmented with additives to promote oxidation over time when exposed to oxygen, heat, and UV light. (Oxidatively biodegrade & Photodegradation)
This causes the plastic to fragment into smaller pieces but not fully degrade. The fragments and pollution from additives were found to have adverse environmental impacts. The process leaves residue in the form of microplastics that enter soils and waterways.
Therefore most countries in the EU, Malaysia, Thailand, New Zealand, Australia, Hong Kong and others have banned Oxo-(bio)degradable plastics due to these issues and because the fragmentation process is not considered true biodegradation. The plastics don't meet standards for compostability or breakdown in natural environments.
Oxo-(bio)degradable plastics are not ideally recycled?
These oxo-(bio)degradable plastics (OBP) materials claim biodegradability, but they would need to meet the requirements of the following tests to claim biodegradability:
- ASTM D5988 (Determining Aerobic Biodegradation of Plastic Materials in Soil)
- ASTM D6954-04 (Testing Plastics that Degrade in the Environment by a Combination of Oxidation and Biodegradation)
Well, in oxygen-containing environments, OBP will eventually degrade and fragment but the plastic itself remains, leaving tiny fragments known as microplastics that can easily enter the environment, oceans, and waterways.
OBP, although technically can be used for recycling, but will negatively affect the quality and the economic value of the plastic recyclates or pellets produced. Many recyclers and converters have reported that OBP cannot be detected by current sorting technology from conventional plastics. For recyclers, it’s extremely difficult to estimate the proportion of stabilizers added and the extent of the degradation induced in the material, so the product is not preferred as it becomes more challenging to maintain the quality of the recycled product with every repeating recycling loop.
Therefore, oxo-degradable plastic packaging is also unfit to be included in the material stream intended for composting. This incompatibility is also clearly stated by many manufacturers of oxo-degradable additives and by the Oxo-biodegradable Plastics Association.
What is bioplastics?What are the examples?
Bioplastics offer hope as an environmentally-friendly replacement for conventional plastics. Derived from renewable resources or a mix of renewable resources and synthetic fossil based materials, they can be either biodegradable or compostable, allowing them to break down fully within months without harming the environment, but the biodegradability depends on their chemical composition and structure.
With further research and development, it is hoped that bioplastics can match the performance of traditional plastics at competitive costs. There is also potential to engineer new bioplastics with even better degradability. Here are some common bioplastic materials currently available as alternatives to conventional plastic, along with what is made of:
PBAT + PLA:
PBAT (Polybutylene adipate-co-terephthalate) & PLA (Polylactic acid), a blend of biodegradable petroleum-based synthetic polymer (PBAT) and a bioplastic derived from fermentation and polymeryzation of corn or sugarcane (PLA). It is generally compostable, commonly found and used as flexible packaging, bags.
PBAT + PBS:
PBAT (Polybutylene adipate-co-terephthalate) & PBS (Polybutylene succinate), a blend of biodegradable petroleum-based synthetic polymer and a bioplastic derived from fermentation and polymeryzation of corn or sugarcane. It is generally compostable, commonly found and used as flexible packaging, bags.
PHA:
PHA (Polyhydroxyalkanoates) produced from microbial fermentation of plant sugars or oils. It is a strong material, compostable, can be found and used as flexible packaging, paper coatings.
PVOH/PVA:
PVOH/PVA (Polyvinyl alcohol), a biodegradable natural gas-based synthetic polymer, can be a bioplastic derived from the fermentation of sugarcane as well. It is dissolvable, compostable, can be used flexible packaging, laundry/tablet film.
The options provide varying levels of biodegradability, strength, and some biobased content to suit different.
Biodegradable is not always compostable?

“Compostable is always biodegradable” however “Biodegradable is not always compostable”
Biodegradable and compostable are terms frequently used to describe environmentally friendly products. Whilst they are both commonly used alongside the description that organic material is broken down in a specific environment in a specific timeframe, it is important to understand that compostability is the term used to describe products that biodegrade under specific conditions.
It can get a little confusing, but the primary difference is that compostable plastics are only biodegradable in specific composting conditions, while the other is a general term used to describe plastics that can degrade in the soil (landfills or anaerobic digesters). “Compostable is always biodegradable” however “Biodegradable is not always compostable” But then, what standards or tests should we look for in order to properly assess these materials?
What are the standard tests to measure the biodegradability of plastics?
In an effort to inform and clarify the various testing methods in use today, and how #INVISIBLEBAG complies with those specifications, let's explore the following standards in more detail.

ASTM D6400
ASTM D6400 covers plastics and products made from plastics that have been designed to be composted in municipal and industrial aerobic composting facilities only. The scope of the specification exists to determine that the products tested will compost at a comparable rate to known compostable materials.
This testing is equivalent to ISO17088. More information can be found on the ASTM Standard website.
EN 13432
The EN 13432 specifies the minimum requirements that a packaging product must meet in order to be successfully processed by Industrial composting methods, which may be the reason why there is an abundance of this testing method in the environmental product community.
The test states a material or product must meet the following requirements;
Disintegration, or fragmentation refers to the visible structure of the product that is left in the final compost. After a 3-month period in a lab prepared setting, the remaining residue for the test material needs to be less than 10% of the original mass.
Biodegradability, the capability of the material to be converted into CO2 under the action of microorganisms whereby over 90% biodegradation must be reached in less than 6 months.
Non-toxic, all components of a material must be disclosed and the amount of heavy metals cannot exceed a stated amount. Furthermore, the remaining compost must not contain toxins or negatively affect plant growth.
A more detailed explanation can be found on the European bioplastics website.
ASTM 5511
ASTM 5511 test covers the biodegradability of plastic products when placed in a high solids anaerobic digester for the production of digestate from MSW (municipal solid waste). This condition may also resemble some conditions in biologically active landfills.
OECD 208
OECD 208 is otherwise known as the seedling growth test which is a continuation from ASTM 5511, whereby the remaining soil that a product has degraded in after 90 days is then used for the testing of seedling growth. For a test to be considered valid, the seedling emergence needs to be over 70% with the seedlings not showing phytotoxic effects.
Steps to follow to make a better choice
In conclusion, packaging that claims to be biodegradable must comply with specific certifications. If you also want to choose truly sustainable products, here are some steps you can follow:
First, do your research before making a decision. Second, ask the company to provide the composition of the materials. Third, partner with a transparent and ethical supplier who can provide certifications. Finally, always ask questions and seek to learn more. Whether you are a brand or a consumer, we can all make smarter and better choices!
To learn more about another bioplastic PLA and compostable packaging, don’t miss our other blog post, “Compostable Packaging: Can it be effectively used in your region?”
...
You may also like:
Compostable Packaging: Can it be effectively used in your region?
How To Dissolve #INVISIBLEBAG?
Zero Waste Home | 5 Home Composters To Reduce Your Food Waste
Microplastics Crisis: From Beach Landscapes to Our Body
Create Circular Future: How V Cycle Empowers Hong Kong’s Seniors Through Recycling
What Can Be Recycled In Hong Kong? A Guide From The Loops Hong Kong
Sources:
Biodegradable. Biodegradable Plastic: Types, Properties & Material Table (Omnexus, 2021)
Government to explore ban on oxo-degradable plastics. (edie.net, 2021)